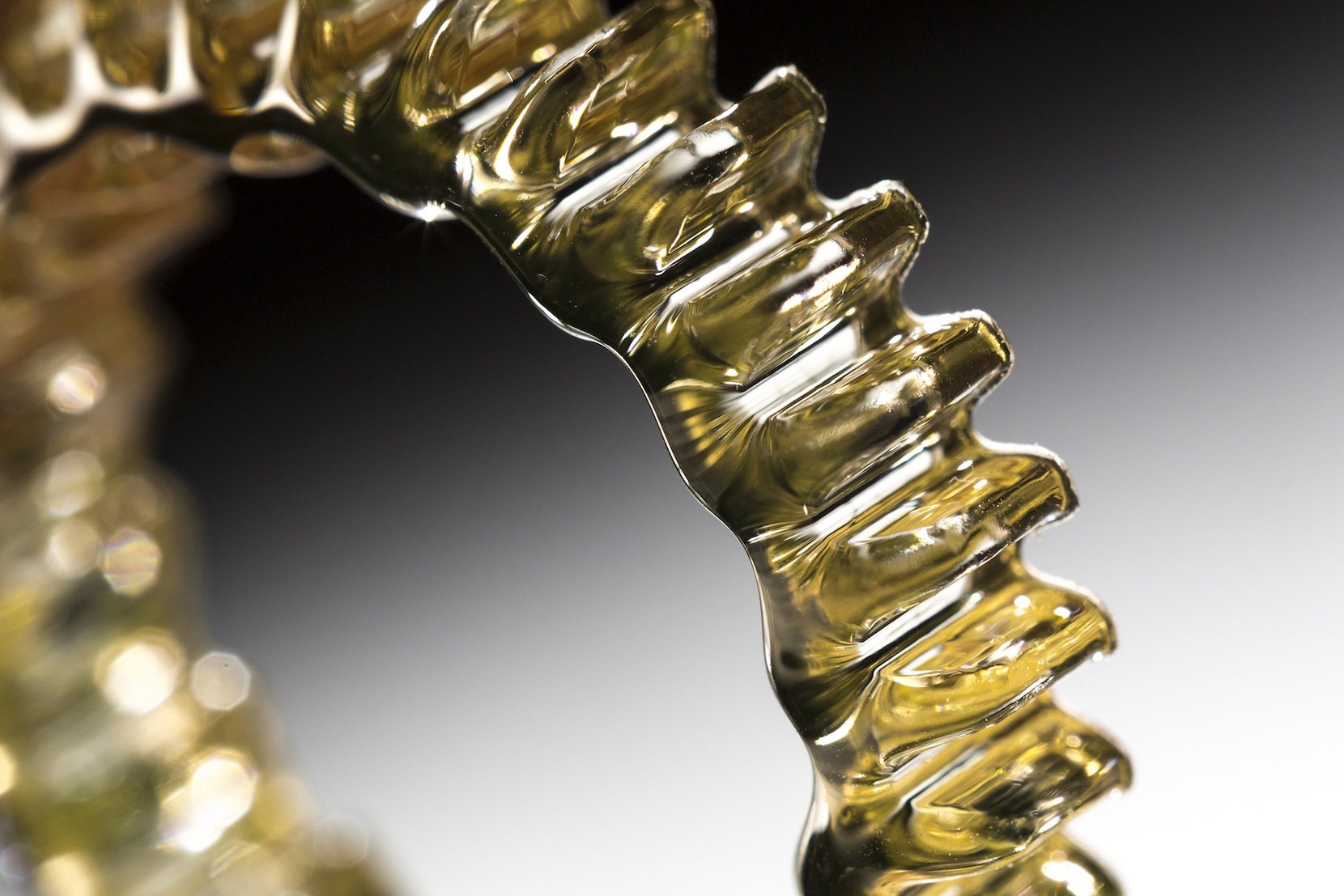
Xaar is inviting visitors to see the latest in printhead technology on stand J21 at this year’s TCT Show, September 25-27 at the NEC in Birmingham. There they can learn how innovations such as Xaar’s High Laydown Technology and our partnerships with industry leading companies help integrators and machine producers to get ahead in 3D Printing.
Jetting 3D fluids with high viscosities (at least 55cP), valuable for 3D printing, is possible with the award-winning High Laydown (HL) Technology. Samples produced with high viscosity photoresins from BASF 3D Printing Solutions will be on display. In addition, significantly increased throughputs can also be achieved with High Laydown Technology. Therefore, faster printing of 3D parts with improved mechanical properties such as tensile strength is possible.
These advantages will be the focus for Angus Condie, Xaar’s Director of Integration and Applications, during his presentation High Volume Manufacturing in Photopolymer Jetting on the ‘TCT Introducing Stage’ on Tuesday, 25 September at 13.50. He will cover in detail how HL Technology can greatly increase the productivity of inkjet-based systems and enable a more diverse fluid portfolio.
In addition to a focus on High Laydown Technology, print samples illustrating how Xaar’s 3D printhead portfolio can be used in various 3D Printing methods such as High Speed Sintering, Binder Jetting, and Photopolymer Jetting will be on display.
“The TCT Show is a major event for the 3D Printing sector and we are excited to be exhibiting for the first time with our 3D printhead portfolio and High Laydown Technology,” says Simon Kirk, Senior Product Manager at Xaar. "We provide continuous support to our customers from early fluid evaluation through to successful
solution development. That’s why we are welcoming manufacturers and integrators to discuss their project proposals and discover how Xaar can help them lower development costs, get to market quicker, and introduce printers that deliver a true competitive edge and a real value to 3D end-users.”